Oil Analysis – Cut Costs and Reduce Downtime
Imagine the consequences of neglecting your lubrication systems
Like a blood test, oil analysis is a powerful tool that gives you the information you need about the health of your engine, including its properties, composition and contaminants. Failure would be both catastrophic and expensive to not only repair the physical damage but from the time taken to find a solution and the revenue lost as a result of equipment downtime.
Lubricating systems management provides a detailed and in-depth view of what’s happening within machinery components during operation and brings a number of benefits to an organisation, including reduced downtime, cost savings, improved customer reputation, reduced wastage and improved health and safety. We discuss how below.
Cost savings and reduced downtime
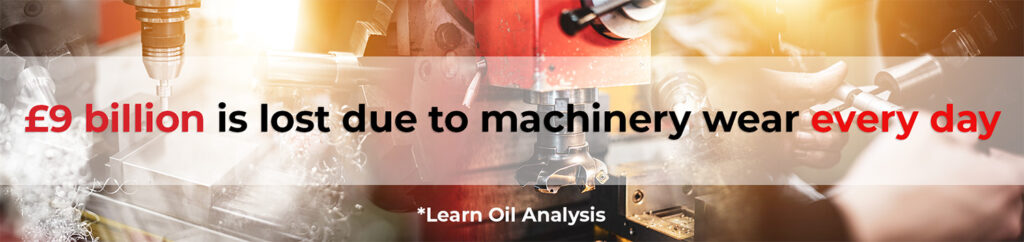
Oil analysis can help pick up any issues to help you avoid a sudden shutdown, with the benefit to cost ratio easily outdoing 10 to 1. Regular analysis allows you to plan maintenance and oil changes so you can ensure your machinery is not idle for unnecessary periods of time.
A proactive and regular lubrication system maintenance programme offers significantly greater savings compared to a reactive programme, helping minimise the risk of costly repairs and unscheduled downtime. It ensures equipment is maintained at peak operating reliability in the most lucrative manner.
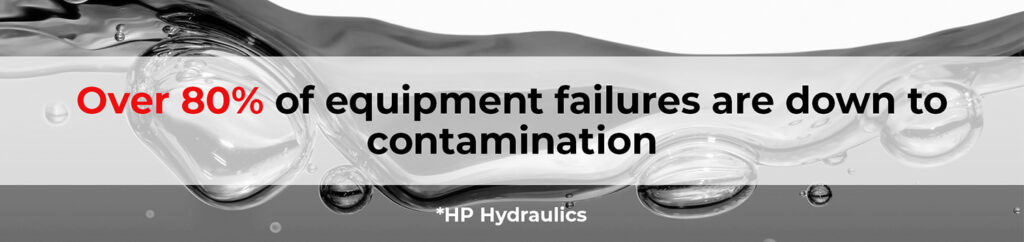
Oil analysis doesn’t mean that a piece of equipment will never fail. All machinery and engines will break eventually, regardless of how much TLC you give them. But when properly implemented, oil analysis can act as an early warning system for lubricating systems; making you aware of any potential problems, such as contamination, before a failure occurs.
Oil analysis and testing most commonly looks at:
Viscosity – the most crucial property of a lubricant due to its significance to oil condition and lubrication. As oil temperature increases its viscosity decreases, leading to lower volumetric efficiency, overheating and wear.
Water – a common contaminant that will have devastating effects such as rust, loss of additive functionality and increased wear rate. This can lead to expensive damage and downtime to high value engines, generators, turbines, gears etc.
Wear metals – such as copper and iron may identify wear in an engine. Wear metal levels will begin to multiply long before machinery displays any symptoms.
Particle counting (PC) – a device that measures the size and quantity of particles in oil, to determine general cleanliness and contamination in oil.
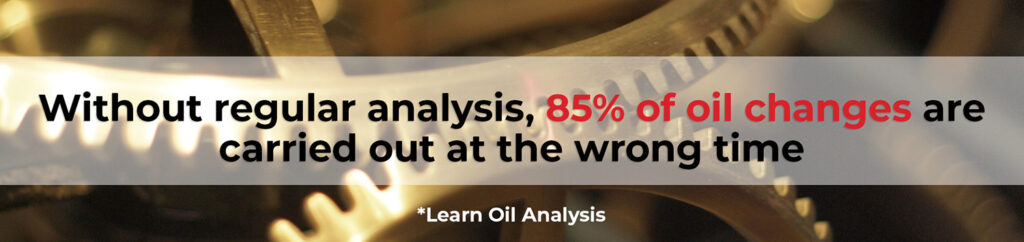
Changing oil sporadically rather than on a regular basis increases the risk of changing oils too early, which is not great for your wallet – or too late, which is not great for your equipment.
Condition-based (proactive) oil changes mean you only change the oil when it’s needed and for the right reason, reducing costs on new oil and waste disposal. This also means there’s less chance of damage to the environment, making more effective use of your resources.
Improved customer reputation
If your machinery fails, it will most likely affect your services and prevent you from delivering on time. Downtime can ultimately damage your name and reduce customer confidence. Regular oil analysis helps head off possible PR disasters before they happen.
Reduced wastage
If the last stage of your production process fails, you risk huge losses, such as intermediate or perishable products. In food production facilities, this could mean a loss of your entire stock records while waiting for a repair.
Improved safety
You can’t put a price on safety. But if oil analysis can save you money whilst improving safety – then great news! Oil analysis helps spot machinery faults and fire risks so they can be fixed before they lead to injury or loss of life.
Are you implementing the best oil analysis program for your lubricating systems?
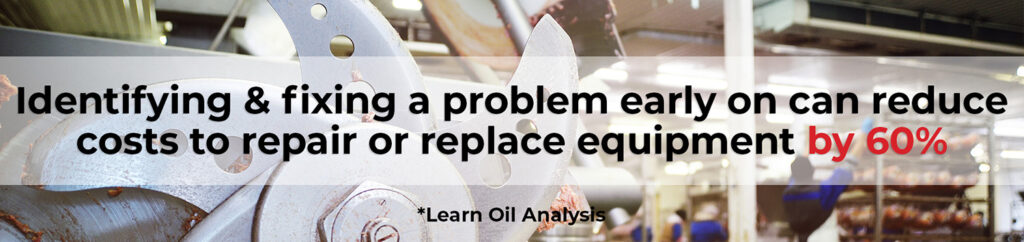
Ask yourself the following…
- Do you have the right quality and type of lubricant for the right application?
- Does your lubricant manufacturer comply with the European and UK Lubricant Industry standards?
- Does your lubricant manufacturer have OEM approvals?
The answers to these key questions will help ensure which tests should be carried out on the oil samples and how often they should be taken.
When was the last time your oils were analysed and tested?
The smooth running and ongoing performance of costly equipment and machinery is critical, which is why we offer all industries a free Lubricant Health Check to help protect your machinery and equipment against wear and tear. Our experts will assess your lubricants at our analysis laboratory to let you know if it’s time to change oils yet.
Book your free lubricant oil analysis today
Take advantage of our oil analysis services to identify any issues within your lubricating systems to help avoid downtime disaster.
Alternatively, call 0330 123 1444 to speak to a member of the team to book your oil test.
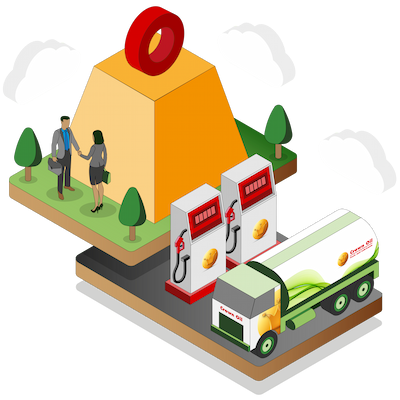